WHY PROFESSIONALS CHOOSE US
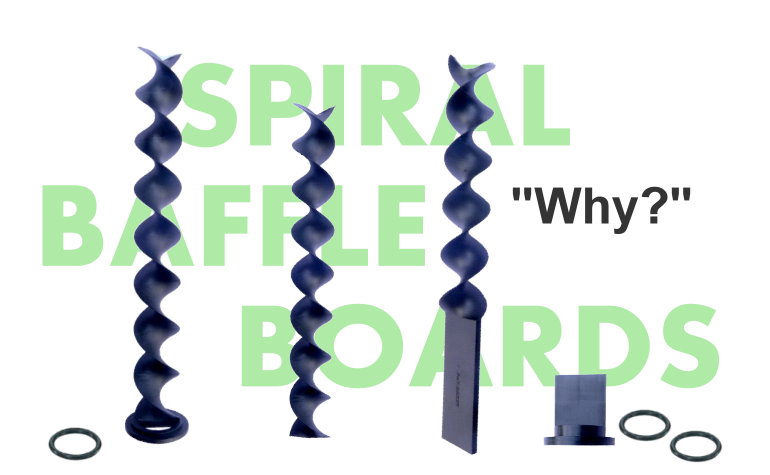
WHY PROFESSIONALS CHOOSE US
The advantages of spiral baffle boards make them an ideal choice for mold cooling systems and they are widely used in the injection molding and blow molding industries. Whether it is to improve production efficiency, save costs, enhance product quality, or extend the lifespan of molds, spiral baffle boards offer significant benefits. Moreover, with the availability of four types - A, B, C, and T - they can be combined to accommodate various mold cooling structures. These advantages have made spiral baffle boards a common and popular choice in mold cooling systems.
If you would like to know more, please feel free to CONTACT us.
Features of Spiral Baffle Boards
Spiral baffle boards are typically made from high-toughness engineering plastics. This enables them to withstand high-temperature working environments of up to 200°C (approximately 392.0 °F) and exhibit excellent durability and long lifespan. The outstanding durability of Spiral baffle boards ensures long-lasting performance and stable cooling effects.
Advantages of Spiral Baffle Boards over Conventional Straight Baffle Boards
- Excellent Cooling Efficiency
The design of Spiral baffle boards allows for the spiral flow of the cooling water within the mold. This spiral flow quickly removes heat from the mold, providing more effective cooling. Compared to traditional straight baffle plates, Spiral baffle boards offer more uniform cooling throughout the entire mold, improving production efficiency and reducing product defects. - Uniform Cooling
The spiral design allows water to flow evenly throughout the entire mold, providing uniform cooling across the mold surface. This helps reduce the occurrence of hot spots and cold spots, ensuring a consistent temperature throughout the mold. - Improved Product Quality
The uniform cooling provided by Spiral baffle boards reduces temperature variations, minimizing internal stresses and potential deformations in the products. This is crucial for producing high-precision and high-quality products, enhancing dimensional stability and overall appearance. - Shortened Production Cycle
The efficient cooling capability of Spiral baffle boards enables faster mold cooling, reducing the cooling time of products. This leads to shorter production cycles, increased production capacity, and improved production efficiency. - Energy Cost Savings
The excellent cooling performance of Spiral baffle boards reduces the cooling time and energy consumption required during the injection molding or blow molding process. This is not only environmentally friendly, reducing energy waste, but also helps lower production costs. - Optimal space utilization
Spiral baffle boards have a compact design, allowing for efficient use of mold space. This provides more flexibility in mold design and allows for the integration of additional mold components.
Why Is The Material Plastic Instead Of Metal?
- Easy Installation and Maintenance
Spiral baffle boards, made from high-toughness engineering plastics, offer easy installation, maintenance, and replacement. Unlike metal baffles, which can rust and are challenging to replace, plastic ones can be easily removed without damaging the mold itself.
Additionally, plastic spiral baffle boards provide a cost-effective and user-friendly solution for mold cooling components. - A Perfect Fit into Water Holes
Spiral baffle boards are made of high-toughness engineering plastic, providing flexibility for a perfect fit into water holes of different sizes.
- Flexible Combination and Application of A/B/C/T Types
The design of spiral baffle boards offers flexibility, the A/B/C/T types can be combined for various mold cooling structures. They can be applied to various types of injection molds, blow molds, and other forms of molds, demonstrating strong adaptability. Whether for small or large molds, spiral baffle boards provide efficient cooling effects.
Comparison
Conventional Straight Baffle Boards | New Spiral Baffle Boards | |
Tooling Method | Complex | Simple √ |
Tooling Cycle Time | Long | Short √ |
Fitting with Tooling | By Case | Good √ |
Water Flow Phenomenum | Laminal Flow | Turbulent Flow √ |
Cooling Effect | Uneven | Even √ |
Price Cost | Higher | Lower √ |
Injection Mold Cost | Higher | Lower √ |
Conclusion |
Production Cost Higher. Part Quality isn't so good. |
Production Cost Lower. √ Part Quality is good. √ |
If you would like to know more, please feel free to CONTACT us.